Why You Should Inspect & Clean Your Fiber Connectors?
Why it is Important to Keep Fiber Optic Connectors Clean?
One of the most overlooked aspects of fiber optic maintenance and troubleshooting is keeping the fiber optic connector endfaces clean. As we will discuss later in this article, a dirty fiber connection can either slow down or completely inhibit network traffic.
Keeping fiber connections clean is different from any other type of cleaning due to the relative sizes of the connectors compared to the particles and contaminants that typically reside on them. Also we need to be diligent in their maintenance by cleaning the connectors every time before they are mated and after each un-mating. Static charges attract dust to the fiber connectors and prevent them from falling off even when blown with a can of compressed air. As we will see later on in this article, dust caps are primarily used to protect the ferrule and do not offer fail safe protection from particle matter. In some cases, the dust caps can actually make a clean connector dirty due to their tendency to keep a static charge. In addition to dust, there are other contaminants like dried liquid compounds that need to be dealt with on the cleanings.
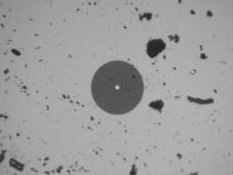
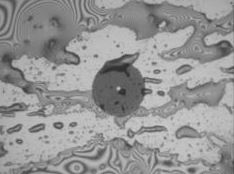
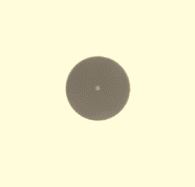
Dust Contamination Liquid Contamination Clean Connector
When troubleshooting fiber, it is important to remember that dirty fiber connections can easily cause a slowdown or a complete shutdown of data traffic. An important tool for a network manager to have is a 200 or 400 power microscope. Dirty fiber connections should not be overlooked when troubleshooting fiber. CAUTION: Never look directly into an illuminated fiber. Laser light can cause permanent eye damage.
Q1: We know that dirty connections can cause attenuation. Can the dirty connections can also cause bit errors and/or slowdown of the network?
Yes, dirty connectors will cause Bit Errors because the contamination degrades the signal quality. In optical networks, the signal comes in the form of a beam of light travelling through the fiber’s core. The fiber’s core has a refractive index value of N1. When the light beam comes into contact with end face contamination, it is now coming entering a second medium which has different refractive index value which we will call N2. The signal experiences changes to both reflection and fraction as it enters the second medium. The signal is basically travelling down the fiber core as a sine wave. The contamination changes that sine wave by reducing the amplitude of the sine wave and spreading its wavelength because of the reflection and fraction that happens when the signal enters the second medium or N2. If you remove the contamination, you keep the light signal in the first N1 medium as it passes between connector 1 to connector 2 eliminating bit error rates.
Q2: Can dirt get between two fibers that are mated if left in a dusty environment? Or will the mating of the connectors prevent any dust from getting on the endfaces?
You do not have to worry about dust nor residue contaminate migration with physical contact connectors as long as they were cleaned before the mating process. The contact region between two mated single fiber connectors is diameter between 250μm to 200μm. When the two ferrules are physically mated, the mating force for most single fiber industry standard connectors is around 1kg or about 2.2lbs. If you calculate the force of what 2.2lbs in a 200μm, that comes to 45,000psi which is why contaminate migration is not a problem even in a dusty environment.
The best way to avoid any chance of contaminate migration is to use a wipe for cleaning unmated connectors on a cable assembly and a stick cleaner for connectors residing in an adapter. The mechanical cleaning tools like the One Click –style cleaners have a limited contact region and will never be able to clean the connector’s end face. The reason is the cleaning tip of a mechanical cleaner have to be able to rotate within the adapter sleeve without getting the cleaning strand or ribbon snagged on the split adapter sleeves. Stick cleaners do not have this problem and offer the largest effective cleaning region. Most cleaning sticks use a different type of cleaning material than the mechanical cleaners are not vulnerable to the snag problems of a flowing cleaning strand in the tools. The stick cleaners are rotated in the adapter sleeve as it cleans the mated connector’s end face. The contact the stick’s cleaning tip makes with the interior of the adapter sleeve during the rotation is helping to pull away dust and connector wear debris that was residing on the interior of the adapter sleeve. This help prevents future particle migration which could land on the ferrule end faces during the mating process.
There is an exception which are the expanded beam contacts. Expanded beam based connectors are starting to gain popularity in enterprise applications because of the Intel MXC connector and in Mil/Aerospace with lens connectors. The connector manufacturers explain that contamination is not a problem because the signal collimates into a large spot size as it passes from the lens of connector A to connector B. An end user would be wise to think about the environment his connectors are being exposed to before assuming he will never have to clean. A large enough piece of dust particulate residing somewhere on either lens will create problems. Also residues have different index of reaction and the amount of residue and its reflective characteristics will cause problems especially at higher data rates. The best practice to avoid long term problems and extend the life of your optical assemblies is to always inspect and remove any contamination regardless of the connector type.
Q3: Is it possible that an end cap (dust cap) can get dirty and cause the fiber endface to get dirty. Should you always clean a fiber when you remove the dust cap, prior to insertion onto a mating sleeve to connect the two fibers?
End caps are c common source of contamination when working with optical connectors. The connector end cap’s primary purpose is to protect the ferrule end face from scratch and pitting defects. It does not protect the ferrule end face from contamination. A customer should never assume that a capped cable assembly is clean when taken out of the bag. Dust and mold release agents are two common contaminates found in end caps.
If a customer gets a new jumper from the manufacturer and inspects it after taking the end caps off, it would not be uncommon to see some small amount of on contamination on the end d face. This does not mean that the jumper manufacturer’s quality process are lacking. All manufacturers experience this. The customer just needs to work smartly and realize that the end cap is just for protecting against scratches. The best practice is to inspect the ferrule, clean if necessary and re-inspect before mating. If the customer does not have a ferrule scope available, then cleaning both connectors end faces before mating will significantly reduce the likelihood of damage and cross contamination.
Q4: Please describe why “wet/dry” cleaning is better that simply either wet or dry cleaning alone.
There are two distinct advantages a wet-dry cleaning process has over the dry wipe process. The first is static dissipation and the second is the cleaning solvent’s ability to loosen up harden contaminates from the ferrule end face without causing permanent defects to the end face.
The dry wiping process that an operator would do using a Cletop style cassette or One Click style cleaner relies on contact friction to remove contamination. When two materials are rubbed together, there is a transfer of electrons between the two surfaces and the imbalance on the surface creates a charged electric force we call static electricity. The two surfaces, one charged positive and the other negative, will try to pull in surrounding particles to being the charge back into a neutral balance. This attraction pulls in the dust particulates in the air and the wear debris on the connector body and adapter. Fiber optic connectors are all dielectric and when they become charged by dry wiping a ferrule act as an insulator storing the electrical charge because there is no dissipative medium for the charge to flow off to. The problem with charged end faces become greater in in low humidity environments. The introduction of a cleaning solvent during a wet-dry cleaning process introduces static dissipative medium for the charge so that it does not stay on the ferrule surface.
Connectors that have been exposed to medium to severe levels of contamination benefit from the introduction of a cleaning fluid. The cleaning fluid will dissolve the harden contamination on a ferrule end face and loosen it up to be wiped away. Dry cleaning only of hardened contamination may require additional pressure by the operator which frequently leads to surface scratches causing permanent end face defects.